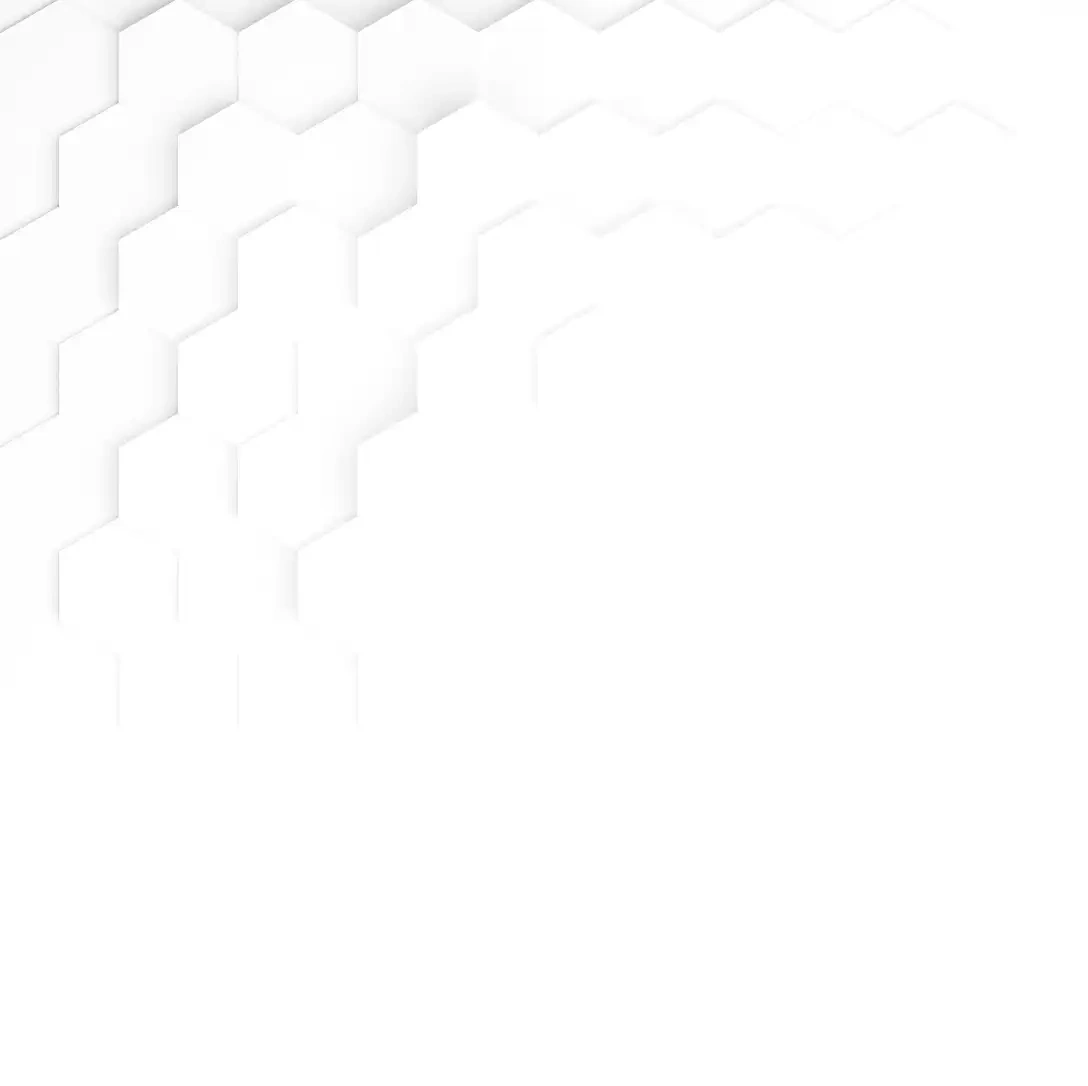
研削加工の仕上げ面不良と改善にお困りの方|ウェットエッチングで解決しませんか?
2024.11.28
研削加工は金属の除去加工として一般的に使用されている方法です。研削加工は金属を砥石で削る加工であるため、細かい加工が施せること、仕上げ面が滑らかになることが大きな特徴です。しかしながら、仕上げ面に不良が起こり、寸法精度の低下や表面粗さが粗くなることもあります。これらは製造歩留まりの低下や製品の低寿命化などを引き起こすこともあり、大きな課題です。本記事では、この仕上げ面の不良の要因と改善方法を解説します。また、ウェットエッチングならばこの仕上げ面不良を解決できることも解説します。仕上げ面不良に悩む皆様のお役に立てば幸いです。
研削加工の仕上げ面の重要性
研削加工は金属の除去加工の中でも、加工精度が高く、仕上げ面の表面が滑らかであるなどの特徴を有します。この章では、研削加工について解説した後、仕上げ面の重要性について解説します。
研削加工とは
研削加工は、金属の除去加工の方法としてよく使用される方法です。金属の除去加工の方法としては、研削加工のほかに切削加工や研磨加工もよく使用されています。これらの違いは、以下の通りです。
- 切削加工・・・「刃物」を用い、金属である工作物(ワーク)もしくは刃物を回転させることで工作物の表面を削り取って加工する方法
- 研削加工・・・「刃物」の代わりに「砥石」を使う方法
- 研磨加工・・・金属を削るという要素の他に表面を磨いて光沢を出す要素も含まれた加工方法
なお、研磨加工では、砥石の他、研磨剤や綿やフェルトなどの布、研磨剤の入ったコンパウンドも使用する
表面の粗さを見ると、切削加工が一番粗く、研削加工が二番目、研磨加工が最も細かくなります。中間である研削加工は、それ単体で金属を所定の形状に加工する以外に、切削加工でおおまかな加工した後に研削加工で表面を整えるという使い方でもよく用いられています。
研削加工は、砥石で除去加工をおこなうことから「精度の高い加工ができる」「表面をなめらかに加工できる」「硬い金属の加工もできる」のが特徴です。
研削加工の仕上げ面は重要
研削加工は、その特徴から工作物の形状を整えるほかに、表面の状態を整え「仕上げ面」の状態を良好にすることも大きな目的です。
この「仕上げ面」の状態が良好でない場合、以下のような現象が起こります。
- 加工精度の低下
- 表面粗さが粗くなる
- 美観の低下
順番に解説します。
加工精度が低下すると、当然のことながら寸法にも影響を及ぼします。寸法精度の低下は、製造歩留まりの低下の大きな原因です。もし、工作物が部品としての品質を保ったとしていても、寸法精度が低めであると、その後の組立工程や組み立てた製品の動作に支障をきたすおそれがあります。また、表面粗さが粗くなることは、工作物である部品表面の摩擦増加の要因です。このような表面の粗さがあると、他の部品と組み立てて動作させた場合に摩耗を起こし製品の寿命を短くしてしまいます。さらに、美観が低下してしまうと、部品の外観が悪くなり品質評価に影響を与えます。これも製造歩留まりの低下の要因です。
よって、研削加工においては、形状を整えるとともに、「仕上げ面」の状態を良好にすることが重要です。では、研削加工における仕上げ面の不良にはどのようなものがあるのでしょう。
仕上げ面の不良|原因と改善策
研削加工の仕上げ面の不良にはいくつか種類があります。ここではその種類と発生してしまう原因と改善法を解説します。
仕上げ面の不良3種
研削加工の仕上げ面の不良は3種類ほどあります。
- 傷
- びびり
- 焼け
順番に解説します。1つ目の「傷」は、研削加工に使用する砥石の不良などにより起こります。砥石の不良としては、「目詰まり」「目こぼれ」「目つぶれ」などがあります。
2つ目の「びびり」は、仕上げ面に周期的な波状の模様が現れる現象です。外部の振動源の影響や砥石と工作物間の相互作用などにより発生します。
3つ目の「焼け」は、研削中に発生する熱が原因で、仕上げ面が変色したり、硬化したりする現象です。
仕上げ面の不良の原因と改善法
この章では、先程の仕上げ面の不良が起きる原因と改善方法を解説します。
傷
仕上げ面の不良のうち「傷」は砥石の状態が大きな要因です。砥石は、「砥粒」「結合剤」「気泡」からなります。砥粒は実際に金属を削る粒です。砥石本体は結合剤で作られており、その中に粒状の砥石が埋め込まれています。つまり、研削加工は、砥石と工作物を回転させながら接触させることで、砥粒が工作物に当たり削り取られる仕組みです。砥石の中には多くの砥粒が含まれており、摩耗して削れなくなった砥石は結合剤から脱落し、次の砥石が露出して継続して研削できるようになっています。さらに砥粒間には気泡が設けられており、削りカスはこの気泡に入って遠心力により排出されます。
「目詰まり」は、この砥石の中の砥粒と砥粒の間に、削ったカスが詰まって固着してしまい、砥石が刃物として使えなくなった状態です。砥石は、本来削れなくなった砥粒が脱落する構造になっていますが、まだ削れる砥粒が脱落してしまう状態を「目こぼれ」といいます。逆に削れなくなって脱落するはずの砥粒が残存している状態が「目つぶれ」です。砥石がこのような状態になると、工作物表面に傷が発生し、加工精度の低下や表面粗さの低下、美観の損失を引き起こします。
すなわち、仕上げ面の不良を改善して仕上げ面を良好な状態にするには砥石の状態を常に管理し、定期的にドレッシングをおこなって砥石の表面を整えることが重要です。
びびり
仕上げ面不良の中の「びびり」は、外部の振動や砥石と工作物との相互作用が原因です。外部の振動に起因するものを「強制ビビリ」、砥石と工作物との相互作用によるものを「自励ビビリ」といいます。強制ビビリは、研削装置自体の振動や周辺の機器の振動により起こるため、抑えるには周辺機器の配置の変更や各機器を固定するための基礎工事が必要です。「自励ビビリ」は砥石と工作物の間で生じる振動の増幅が原因です。加工時には砥石と工作物の間にうねりが起こります。このうねりは、目詰まりや目こぼれといった砥石の状態が原因で加工回数を重ねるごとに増幅されます。これが自励びびりの原因です。自励びびりを抑えるには、砥石の状態を常に管理し、定期的にドレッシングをおこなって砥石の表面を整えることが重要です。
焼け
研削加工中には、砥石と工作物の間に熱が生じます。これが「焼け」の原因です。砥石と工作物間の熱は、砥石の状態や回転数の速さなど加工条件に応じて発生します。焼けを抑えるには、砥石の管理や加工条件の策定、適切な冷却液の使用などが有効です。
このように研削加工の仕上げ面を改善するには、傷やびびり、焼けを抑える必要があります。
仕上げ面の改善をおこなう場合のデメリット
傷やびびり、焼けを抑えて仕上げ面を改善しようとすると、多くの手間と工数が必要です。例えば傷や自励びびりを防止するには、砥石の目詰まりや目こぼれ、目つぶれを防止するべく適宜ドレッシングをおこない、常に砥石が一定条件で削れるように管理しなくてはなりません。強制びびりを防止するには、各機器の配置の変更や機器を固定する基礎工事など時間と費用のかかる工数を踏まなくてはなりません。焼けを防止するために、加工に合わせた冷却液を使用すれば設備の投資や廃液の処理などの手間が増えます。
いずれの方法も、生産コストに上乗せせざるを得ません。また、工数が増えることから時間がかかり、生産速度や生産効率の低下を招きます。とはいえ、製品の品質を担保することは必要です。
仕上げ面の改善にはウェットエッチングがおすすめ
研削加工の仕上げ面にお悩みのみなさま、目詰まりなどによる傷やびびり、焼けが生じず、ある程度のレベルの仕上げ面が得られるウェットエッチングを検討してみてはいかがでしょう。
エッチング加工とは
金属のエッチング加工としては、溶液を用いた金属の溶解現象を利用して不要な金属部分の除去加工をおこなうウェットエッチングが一般的です。
ウェットエッチングでは、機械的な加工よりも細かい加工を施せます。自動車の部品などの比較的大きな部品はもちろん、半導体や電子回路など微細な部品で比較的精密な加工が必要な分野で多く使用されています。
ウェットエッチングは、比較的低コストでエッチング加工ができ、大量生産にも向いている方法です。
それでは、ウェットエッチングについて詳しく解説します。
ウェットエッチングとは
ウェットエッチングは、先ほども解説したように金属が薬品に溶解する現象を利用したエッチング方法です。例えば金属板に丸い穴を開けたい場合は、穴を開ける部分以外を溶けないように保護します。そして、保護されていない露出している金属部分だけを溶解して穴を開けます。
詳しい工程は、以下の通りです。
- パターンフィルム(露光用原版)を作成する
パターンフィルムは、エッチング加工する金属板に保護膜を作成する際に被せるフィルムです。フィルムには、作成するパターンと同一の形状が作製されています。例えば、金属板に丸い穴を開けたい場合は、所定の位置に丸い穴パターンがあるフィルムを作成します。 - 金属板の準備・前処理をする
金属板表面をきれいにして後工程のフォトレジストの密着度を高めます。具体的には脱脂や酸洗および水洗などをおこない、金属板表面に付着している油分やほこりを取り除くとともに、金属板表面を活性化させます。 - 金属板の上にフォトレジストを成膜する
例えば、フィルム状のフォトレジストをラミネートしてフォトレジスト層を成膜します。 - パターンフィルム(露光用原版)をフォトレジストに被せる
- フォトレジストを露光させてパターンフィルムの形状を転写する
フォトレジストに光を当てると、パターン形状通りに露光されます。 - フォトレジストを現像する
現像すると、フォトレジストで覆われていない部分の金属面が露出します。 - 薬品で溶解する
金属板の露出している部分を薬品で溶解し、除去します。 - フォトレジストを除去する
金属板を保護していたフォトレジストを除去し、所定のパターンが形成された金属板を取り出します。 - パターンが形成された金属板を洗浄および乾燥する
金属板の洗浄・乾燥をおこなうとともに、品質検査を実施します。
以上のような工程を経てウェットエッチングによる加工がおこなわれます。
先ほど申し上げたように、金属のエッチング加工の方法としては、ウェットエッチングが一般的です。エッチング加工には、ドライエッチングという方法もあります。ドライエッチングは、穴部分や所定の形状以外の部分をプラズマを用いて除去加工をする方法です。具体的には、エッチングガスをプラズマ化して生成されるイオンや高速中性粒子、ラジカルなどを金属に接触させて不要部分を除去します。ただし、このドライエッチングには、装置が大掛かりになるという課題があり、ウェットエッチングほど汎用性が高いとは言えません。
実際に加工業者を調査したところ、ウェットエッチングをおこなう業者が多く、金属加工をおこなう際にはウェットエッチングを用いるのが一般的だといえるでしょう。
工程をみてわかるように、ウェットエッチングでは機械的な加工を施さないため、研削加工における仕上げ面のトラブルは発生しません。
ウェットエッチングなら良好な仕上げ面を確保できる
ウェットエッチングでは物理的な加工をおこなわず、化学的な方法で除去加工をおこなうため、研削加工で生じるような仕上げ面のトラブルが発生しません。
よって、研削加工のような仕上げ面の改善をおこなう必要がなく、目詰まりなどを起こさないための砥石の管理やびびりを起こさないための機器を固定する大掛かりな基礎工事は必要ありません。また、熱を抑えるクーラント処理も不要です。
これらのことからウェットエッチングで加工すれば、研削加工のような仕上げ面のトラブルが生じず改善を行う必要もなく、ある程度のレベルの仕上げ面を得ることが出来ます。
金属へのエッチング加工なら豊富な技術・経験を持つ株式会社ケミカルプリントへ
研削加工の「仕上げ面」の仕上がりや改善にお悩みの方、ウェットエッチングでの加工を検討なさってみてはいかがでしょう?
株式会社ケミカルプリントは、60年にわたりエッチング加工をはじめとした金属加工に向き合っています。60年の間に様々な用途や品質基準をクリアしてお客様のご要望に応えてきました。経験に裏打ちされた技術・経験や実績は、きっとお客様のお役に立つことでしょう。
株式会社ケミカルプリントは、微細・極小・極薄製品の加工を得意としています。特に5ミクロン厚の極薄製品や、0.1mm未満の穴あけ加工など加工限界を狙ったエッチングを高精度で提供しているのが特徴です。
経験豊富であることから、加工方法についても知識や技術を多く持ち、オーダーされた方法以外の方法を提案する提案力も持っています。実際の加工も熟練したスタッフが高い技術力で効率的におこない、お客様にご満足頂けると思います。
ウェットエッチングによる金属加工をお考えなら、株式会社ケミカルプリントに相談なさってみてはいかがでしょう?
まとめ
金属の研削加工の「仕上げ面」の仕上がりや改善にお悩みの方、一度ウェットエッチングでの加工をご検討頂いてはいかがでしょう?
その際には、60年にわたってエッチング加工をおこなってきた信頼のおける株式会社ケミカルプリントに相談してみてください。きっと、あなたのご期待に応えられると思います。