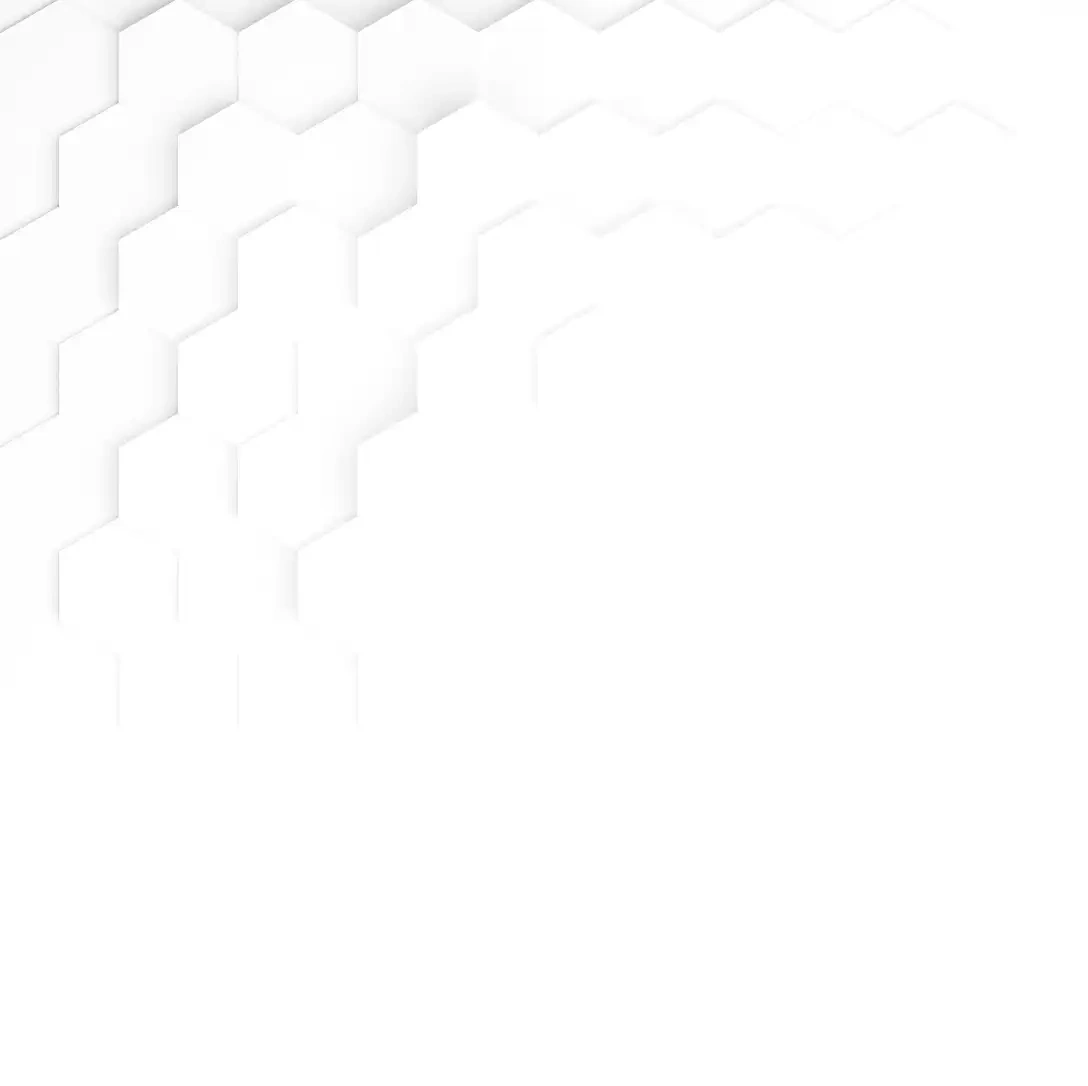
切削加工に用いる工作機械とできる加工、適している材料について解説
2024.10.18
切削加工とは、金属や樹脂等の材料を工作機械で削って加工する方法を指します。一口に切削加工と言っても使用される工作機械の種類は行いたい加工によって様々です。今回の記事では切削加工で用いる各工作機械がどのようなものか、各工作機械ができる加工について解説していきます。また、最後に切削加工に向いている材料と向いていない材料についてもご紹介します。
本記事では切削加工の工作機械で主要と考えられる旋盤、フライス盤、中ぐり盤、ボール盤、マシニングセンタを解説していきます。
切削加工に用いる旋盤とはどのような工作機械か
数多くの工作機械の中でも、旋盤は最も基本的な工作機械です。旋盤は、回転する材料に工具(刃物)をあてることで加工を行います。使用する工具(刃物)の種類や動かし方で様々な加工をすることが可能となっており、一般的に外径加工、内径加工、端面加工、ネジ加工、溝加工、穴加工等の加工ができます。
旋盤の種類は多く、普通旋盤、立て旋盤、卓上旋盤、タレット旋盤、CNC旋盤、CNC自動旋盤などがあります。加工可能な工作物サイズによって適切な機械サイズが求められ、小型から大型までの機械があります。
旋盤によって可能な加工
旋盤で加工可能な形状は、材料が回転することを前提にしているため、主に円筒形等の形状に限定されます。具体的には、以下のような形状に加工することができます。
・円筒形
基本的な形状です。棒材や円盤状の材料を旋盤で回転させ、バイトを使って表面を削ることで、直径が一定の滑らかな円筒形を作成できます。
・円錐形
円筒形の一方が太く、もう一方が細くなる円錐形も旋盤で作成可能です。
・球体の加工
円筒形等の旋盤による加工より技術を要しますが、球体の加工を行うことも可能です。
切削加工に用いるフライス盤はどのような工作機械か
フライス盤は旋盤と逆で工具を回転させて加工を行う工作機械です。フライス盤は平面方向の切削が得意で、凹凸のある面を平らにしたり、段差をつけたり、溝をいれたり、穴を空けるような加工に使用します。フライス盤にも種類が多くあり、立型フライス盤、横型フライス盤、万能フライス盤、汎用フライス盤、NCフライス盤と用途等によって使用するフライス盤が異なってきます。
フライス盤によって可能な加工
フライス盤による加工は、行いたい加工によって工具を変える必要があります。フライス盤による加工では平面や側面を削る加工が一般的ですが、下記の4つの加工も可能です。
・段差加工
平面と側面を同時に削っていき段差の形状に加工します。
・溝加工
対象物に溝を掘る加工です。
・穴加工
フライス盤では、ボール盤で加工するような対象物に穴を空ける穴加工を行うこともできます。
・3次元加工
従来のX軸、Y軸の平面的な加工に立体的な奥行きであるZ軸を加えた加工を指します。コンピューターで制御し、3次元のより高度な形状の加工が可能です。
切削加工に用いる中ぐり盤はどのような工作機械か
中ぐり盤とは中ぐり加工に特化した工作機械のことを指します。中ぐり加工とは穴が空けられた対象物に対して、その穴を内側からさらに削って加工することを言います。
中ぐり盤は、切削工具を回転させながら対象物の穴を広げる等の加工をしていきます。加工精度の高い穴を対象物に空けたい場合や、大きい穴を空けたい場合に適している工作機械です。
中ぐり盤も種類が多くあり、横中ぐり盤、立中ぐり盤、ジグ中ぐり盤、NC中ぐり盤と用途等によって使用する中ぐり盤が異なってきます。
中ぐり盤によって可能な加工
中ぐり盤は中ぐり加工に特化した工作機械であるため、対象物の穴をさらに削って広げる等がメインの加工となります。一方でフライス加工も行うことができるため「主なフライス盤によって可能な加工」の内容もご参照下さい。
切削加工に用いるボール盤はどのような工作機械か
ボール盤は工作の対象物に対して穴を空けたりするための工作機械です。使用する工具を適切に選んで多様な加工を行える点も特徴の1つです。旋盤やフライス盤でも穴あけ加工を行うことは可能ですが、ボール盤は中ぐり盤と同様に穴をあけることに特化した工作機械と言えます。
ボール盤にも種類が多くあり、直立ボール盤、卓上ボール盤、多軸ボール盤、ラジアルボール盤、深穴ボール盤、タレットボール盤と用途等によって使用するボール盤が異なってきます。
ボール盤による加工可能な形状
ボール盤は取り付ける切削工具によって多様な加工が可能となります。一般的な加工の例をご紹介します。
・穴あけ加工
ドリルを用いて対象物に穴をあける加工です。
・中ぐり加工
対象物に空いている穴の内径を広げて寸法精度を高める加工です。
・座ぐり加工
「座ぐり」とはネジ等の頭部飛び出しを防ぐために凹みをつくる加工です。
・リーマ加工
穴の内径を薄く削ることで対象物に空いている穴の精度を高める加工です。リーマと呼ばれる切削工具を用いて加工します。
・ねじ切り加工
対象物に空いている穴へタップという工具を用い、めねじのねじ山を作る加工です。
切削加工に用いるマシニングセンタはどのような工作機械か
マシニングセンタとは自動で切削工具の交換ができる機能を有している工作機械です。加工プログラムに沿って自動で工作機械を交換し、フライス削り、中ぐり、穴あけ等の切削加工を1台で行うことができます。マシニングセンタは1台で複数の加工が可能なため、作業効率が向上することや、自動で加工するため加工精度の改善等が見込めます。
マシニングセンタにも種類がいくつかあり、立型マシニングセンタ、横型マシニングセンタ、門型マシニングセンタ、5軸制御マシニングセンタと用途等によって使用するマシニングセンタが異なってきます。
マシニングセンタによる加工可能な形状
マシニングセンタは複数の切削工具を使用できる工作機械です。そのため、フライス削り、中ぐり、穴あけ等のこれまでご紹介してきた旋盤以外の工作機械が行える加工を1台で実施することが可能です。また、5軸制御のマシニングセンタであれば複雑な形状の加工を行うことも可能です。
切削加工に向いている材料と向いていない材料
切削加工に用いる工作機械も加工方法も様々ですが、加工する材料の向き不向きというものもあります。最後に切削加工に適している材料と適していない材料についてご紹介します。
(切削加工に向いている材料)
・鉄鋼材料
鉄鋼材料は鉄を主成分とし、炭素やマンガン、ケイ素等の様々な元素が含まれています。鉄は組み合わせる元素や熱処理によって硬くすることや、柔らかく加工がしやすくなる等の機能的特性をコントロールできる特徴があります。また他の材料よりも安価な傾向のため、ものづくりにおいて使用される頻度が高い材料の1つです。切削加工による加工もよく行われ、適している材料の1つと考えられています。
・アルミ合金
アルミ合金とはアルミニウムに他の金属をプラスして作った材料のことです。アルミ合金の代表的な性質としては軽さや加工のしやすさがあり、切削加工に向いている材料と考えられています。一方で、純粋なアルミニウムは靭性が高いため切削加工には向いていない材料と考えられています。
・黄銅
黄銅は銅と亜鉛からなる合金で5円玉などに使われている金属材料です。黄銅の性質として優れた伸展性、切削性の高さ等があり、合金の中でもとりわけ加工がしやすいと言われています。鉄鋼材料やステンレス鋼よりも切削性が良いと考えられており、切削加工に向いている材料と考えられています。
・樹脂材料
樹脂材料(プラスチック)は大きく分類して「熱可塑性樹脂」「熱硬化性樹脂」の2種類に分けられます。樹脂材料の切削加工に用いられるものは「熱可塑性樹脂」が大半です。金属などの材料と比べ熱伝導率が低いため、熱の影響を受けやすい傾向にあります。そのため、加工時には摩擦による熱を考慮して加工する必要等があり、切削加工ができる材料ではありますが、加工の難易度は高いと考えられています。
(切削加工に向いていない材料)
・ステンレス鋼
ステンレス鋼は鉄を主成分とし、炭素、クロムを含んでいる合金鋼です。ステンレス鋼は強度・硬度が高く、耐熱性・耐食性も高いという性質を有しています。そのため、ジェット機に用いるタービンブレード等の重要な部品をつくる際にステンレス鋼が使われることもあります。一方で、強度・硬度が高く、耐熱性・耐食性も高いという性質から加工時間が長くなるデメリットがあり切削加工に向かないと考えられています。
・その他難削材
切削加工に不向きな材料は難削材と呼ばれています。硬度が高く削りにくい、熱伝導率が低く加工時の温度を逃がしにくい、脆性があり加工時に壊れやすい等の特性を持つ材料が一般的に難削材に分類されます。
硬度が高い材料の例としてチタンやタングステン、熱伝導率が低い材料の例としてはステンレス、脆性があり加工時に壊れやすい材料の例としてはセラミックやガラスがあります。
上記の材料は一般的に難削材に分類されますが、メーカーによっては加工が可能なケースもあります。
まとめ
今回は切削加工に用いる工作機械について解説しました。各工作機械によって様々な加工が可能であることがお分かりいただけたかと思います。一方で切削加工にもデメリットや不向きな加工、材料があるためそれを把握して適した手段を選ぶことが重要です。
切削加工のデメリットについてはこちらの記事を確認してみて下さい。
また、同じ材料でも加工対象の厚みや生産ロット数によって異なる加工方法の方が適しているケースもあります。例えば、薄いステンレスに対してある程度の数の加工を試みる場合、切削加工では1つの加工に時間を要するため非効率になってしまうケースもあります。そのようなケースにおいて、エッチング加工であれば高精度かつある程度の数の加工を行う際に効率よく加工をすることができます。
どのような厚み、材料、生産ロット数であればエッチング加工がメリットがあるかは様々なケースがあります。もしエッチング加工が適している加工ニーズがある際には是非一度ご検討ください。
その際には、60年にわたってエッチング加工をおこなってきた信頼のおける株式会社ケミカルプリントに相談してみてください。きっと、あなたのご期待に応えられると思います。